We ended up building three different structures in total, the third being kind of a mix between the diamond-shape first and the organically grown second one. While our first attempt was more like a hands-on-solution, we tried to use the results of our SKO-calculations in a second attempt. The (more or less) final structure could be seen as a result of our findings from the previous experiments and also meets our self-set standards of not using a second fixation and still managing the torsional forces over long distance.
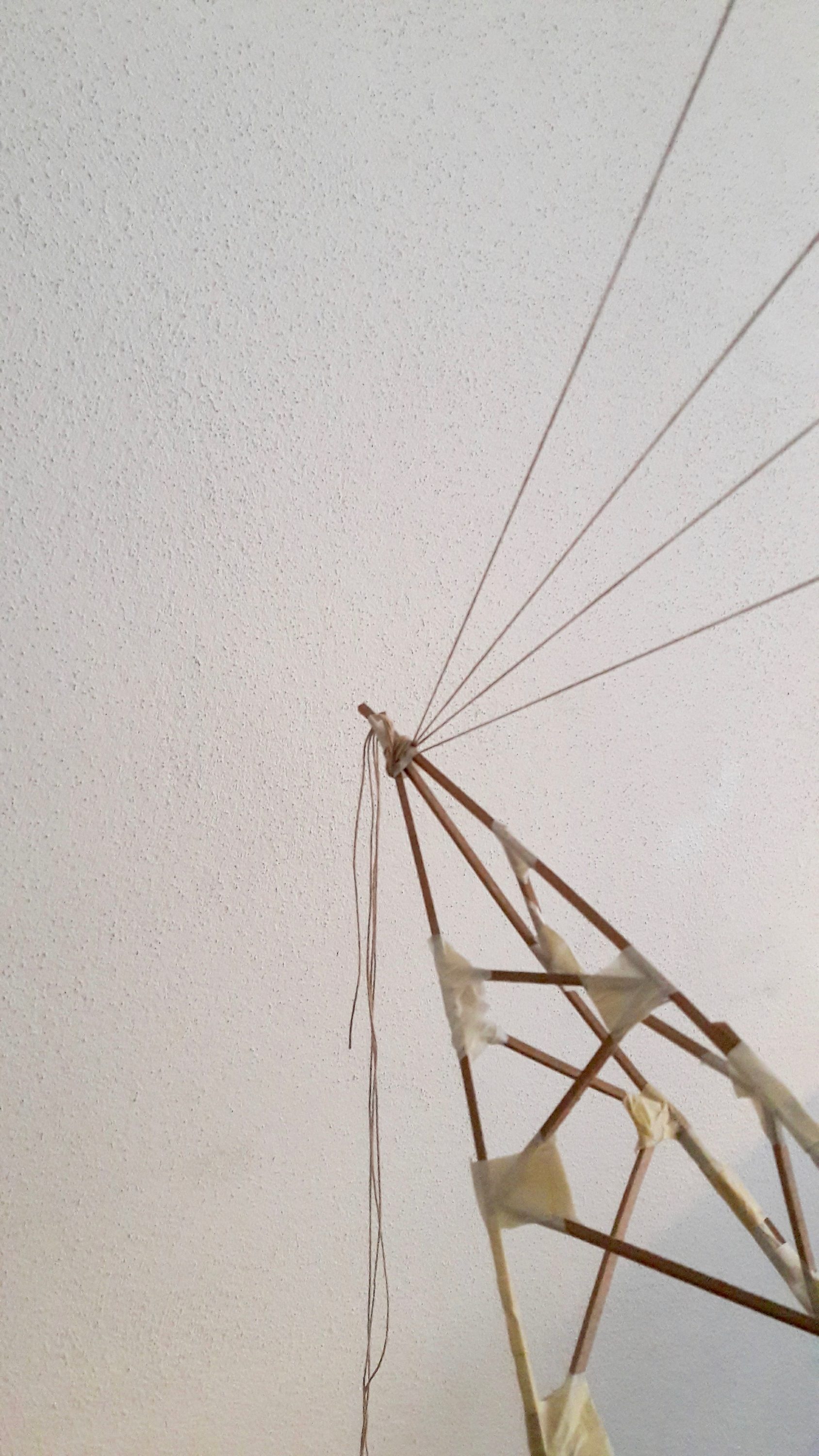
+